Recent studies tying subsurface stress conditions and mechanical properties of rocks to physical processes are providing a glimpse into the best methodologies to stimulate a reservoir to maximize fracture network complexity.
Using a geomechanical approach to fracture characterization has revealed that continuous pumping completion systems (e.g., ball-activated systems) achieve higher fracture complexity and surface area in the reservoir, resulting in higher drainage efficiency when compared to startand- stop completion systems (e.g., plug and perf).
Hydraulic fractures are typically modeled as a single fracture because only one set of treatment measurements is available, such as treating pressure. The surface pressure response, treatment rate and proppant concentration are translated into a single planar fracture with a corresponding height, length and width. This can be a gross oversimplification of the actual fracture complexity.
This model also does not take into account continued deformation of the rock mass over a longer time period. During stimulation the reservoir is forced to accommodate additional volume. Time-dependent strain of the rock mass is typically not considered once a stage has been sealed off in the wellbore and operations have moved on to the next stage.
Key mechanisms controlling stress redistribution are the magnitude of the stress differential within the fracture relative to the minimum stress and the rocks’ ability to accommodate it through elastic and inelastic processes.
If there is a time lag associated with operations, it is impossible to apply additional strain before energy loss and fracture closure begins. In a continuous pumping operation, the timing enables added stress to the system before the first initiated fracture is in a mode of closure.
Start-and-stop versus continuous pumping
Operational differences between completion methodologies impact geomechanics, stress distribution and fracture complexity, which ultimately correlates to reservoir drainage.
As slurry enters the reservoir for the first stage, the rock mass is forced to accommodate additional fluid and proppant. The resulting fracture adds pressure along the fracture face. The dissipation of this pressure manifests as a stress shadow that extends out into the surrounding rock through leak-off, elastic strain and inelastic strain. At this point in the treatment, the stress mechanisms are identical for both completion methodologies.
In start-and-stop completion operations, energy is lost from the fracture system after the first stage. The well is flushed to displace proppant remaining in the wellbore, ensuring that wireline tools are not obstructed. Tools for the next stage are pumped down using additional fluid that displaces proppant from the fractured interval. Perforating the next stage creates a new leak-off path for excess pressure from the previous stage’s fracture. Excess stress in the fracture can equalize within the wellbore and reservoir. This equalization, or redistribution of stress, allows fracture closure.
Small losses in energy from the area of interest can have tremendous impact. The net effect of a change in the proppant distribution and stress dynamics are shorter and fewer complex fractures with less near wellbore conductivity.
In continuous pumping completion operations, stress in the local rock mass is at a maximum and the continuous addition of fluid to the system can be seen as the addition of energy. Following the first stage, spacer fluid is pumped down, followed by an actuation ball to isolate the previous stage and immediately begin operations for the second stage. When the ball lands in the sliding sleeve, the next stage is treated without interruption.
These operations eliminate stress redistribution. The timing of the next fracture is at a point that can maximize and retain stress in the stimulated rock, leading to further ranging stress shadow effects (see Figure 1 above).
Since continuous pumping completions are in a continuous mode of fracture propagation by virtue of the uninterrupted addition of fluid, the stress shadow interactions between sequentially created fractures are maximized. The second fracture further alters the stress state, and the stress shadows associated with each fracture have an additive effect on the rock mass between the fractures. The benefits of this process include added fracture complexity and improved drainage efficiency through greater fracture surface area.
Case studies
A study from a group of wells in the Montney Formation of the Western Canada Sedimentary Basin indicated fundamentally different geomechanical processes in start-and-stop and continuous pumping completions. The continuous pumping completions achieved higher EUR by more than 40% compared to the start-and-stop completions.
In addition to the production study, analysis of microseismic interpretations showed distinctive differences between the events recorded in each type of completion. The study’s conclusions included
- A significantly greater number of seismic events occurred in wells using continuous pumping completions systems, and larger magnitude microseismic events occurred at all distances from the well;
- Strong fracture complexity was evident in the wells using continuous pumping completions but not in the start-and-stop wells;
- Lower magnitude focal mechanisms in start-and-stop wells indicated that these treatments followed preexisting fracture pathways rather than developing new planes of failure; and
- The increase in production was directly related to the development of new fractures identified from microseismic data (Figure 2).
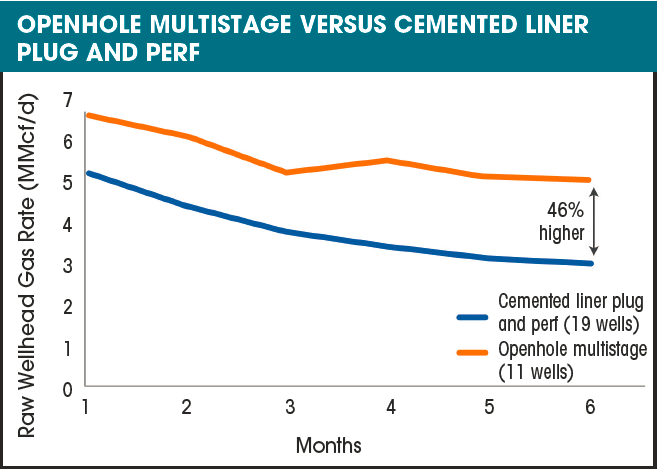
Another study in the Montney Formation examined the impact of continuous pumping completions fracture propagation on a producing well from two offset wells using microseismic data and a simulation model.
Well 1 was a producing well, and Well 2 and Well 3 were completed using a continuous pumping completion system. All 16 stages of Well 2 were completed in two days. The first 15 stages of Well 3 were completed the following two days, and then the final five stages of Well 3 were completed after an 11-day shutdown.
The results of the observations and simulation analyses offered insights:
- Production depletion can affect the stress in adjacent rock volumes, even if they are hydraulically isolated from the producing wells. This affects the stimulation patterns of completed wells;
- The prolific fracture propagation pattern of Well 3 likely resulted from the stress shadow influence of Well 2 and the rapid execution of successive stages in Well 3; and
- Stress shadow influences on the final five stages of Well 3 were absent because of the long interruption of operations, which was due to stress redistribution.
Conclusion
Studies examining stress mechanisms in the reservoir during stimulation showed clear differences between continuous pumping and start-and-stop operations.
The rapid sequential execution of stage treatments was beneficial to managing fracture propagation. The continuous pumping completions resulted in higher fracture complexity because they did not allow time for pressure in the hydraulic fracture to dissipate through the reservoir.
Furthermore, the stress shadows created by the fracture system of each stage had an additive effect, contributing to higher fracture complexity and improved drainage efficiency.
No comments:
Post a Comment